About Onboard Fish Handling
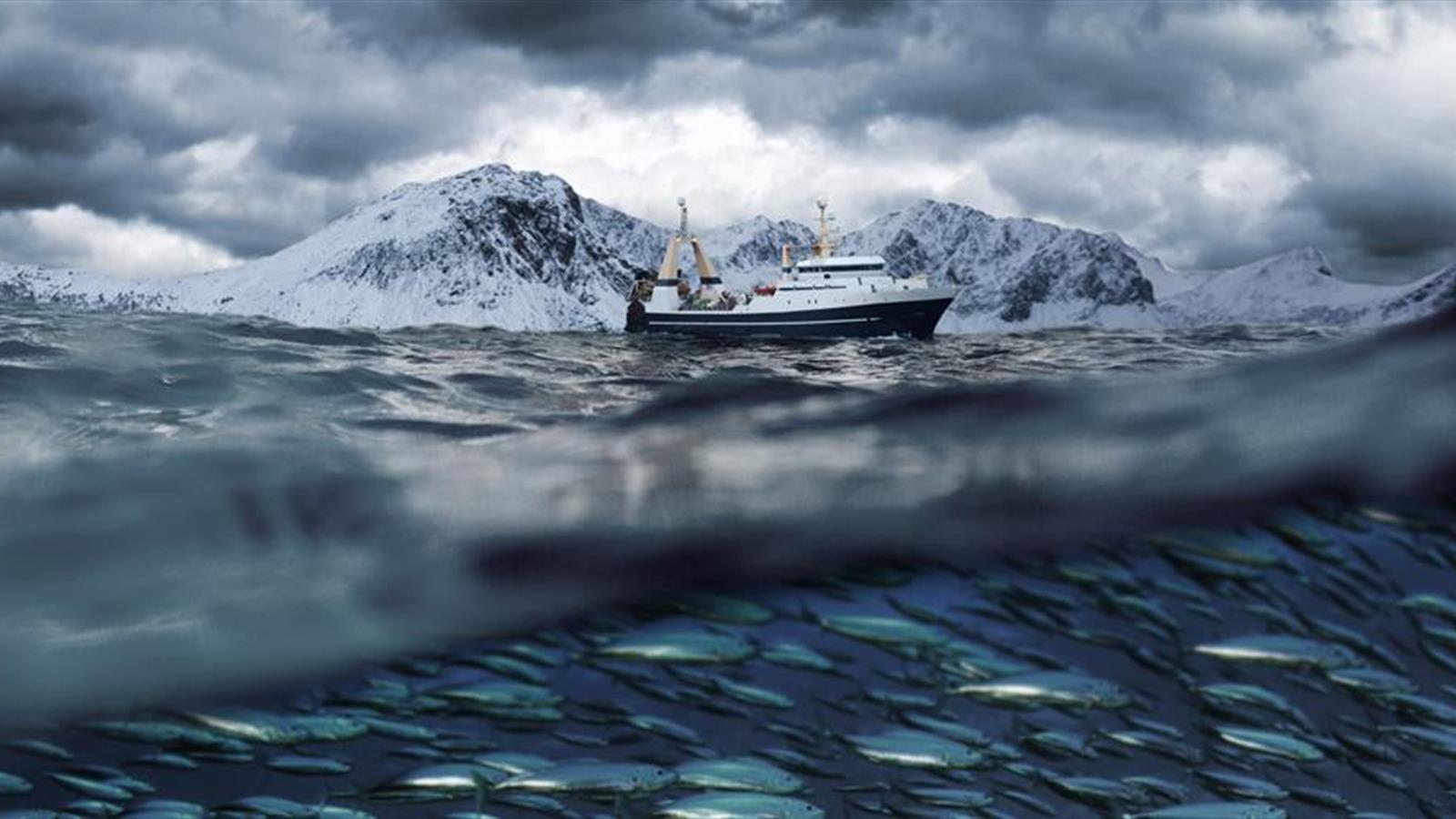
Care for fish and quality
High quality fish products are made from high quality fish handling. From the moment the fish is brought on board the ship it is vital to secure its wellbeing. Optimar's automated systems maintain a high level of animal welfare as well as save time, energy and money.
Our robust equipment can meet our customers' needs in the most extreme conditions, where every minute counts and downtime is no option.
Design
Solutions, design and engineering
Optimar is known for it's ability to analyze technical challenges that call for a combination of engineering disciplines.
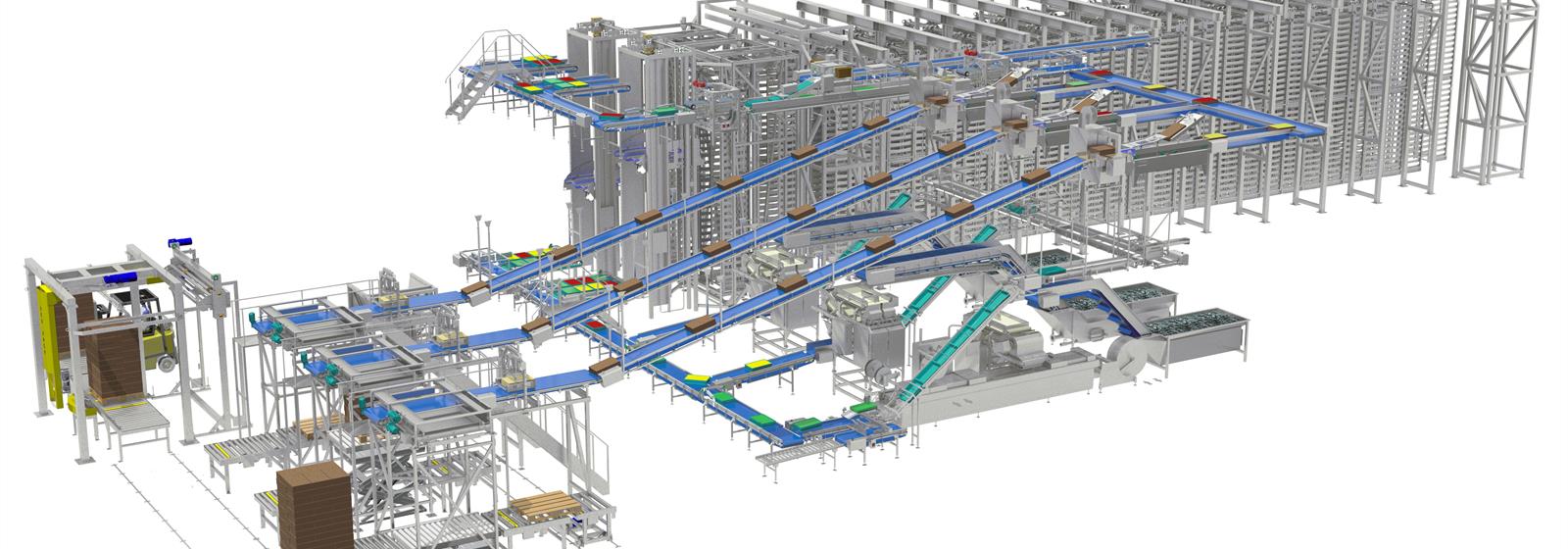
Optimar customers know our machines work in extreme conditions ? they know we do too!
The depth and breadth of expertise needed to explore solutions for you is, literally, under our own roof. This expertise ranges from production logistics and design to civil, electrical and mechanical engineering to automation and programming development.
Optimar designs it's own equipment to interface with any other solution currently available. This means you don’t need to decide in advance the suppliers of your other process-specific solutions. It also means we can work together to choose the technology that best fits the product, the functionality and your price range. Our designers work with you to define specifications and a strategy for implementing them. We design and fabricate standardized as well as customized systems and we have a catalog of contacts to help you select other suppliers for other equipment.
To help make your plans a reality, our skilled engineers can serve as project managers if you need one, or they will work closely with yours if you have one. In either case, Optimar is your partner for the long-term. Flexibility, quality, and reliability define the goals of Optimar’s team of experienced, creative engineers. They work closely with you to find the best, most reliable, most cost-effective solutions to strengthen your competitive advantage.
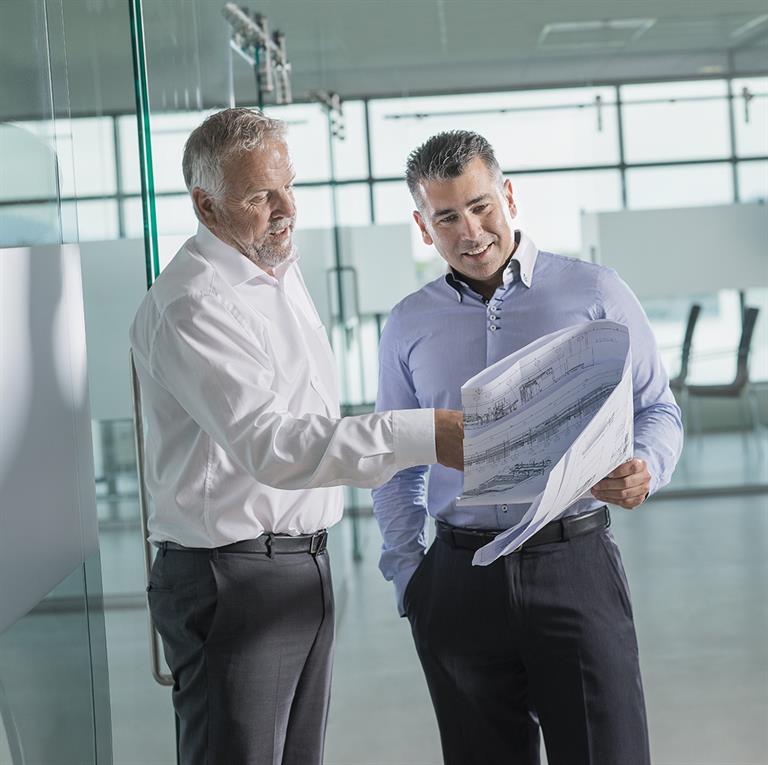
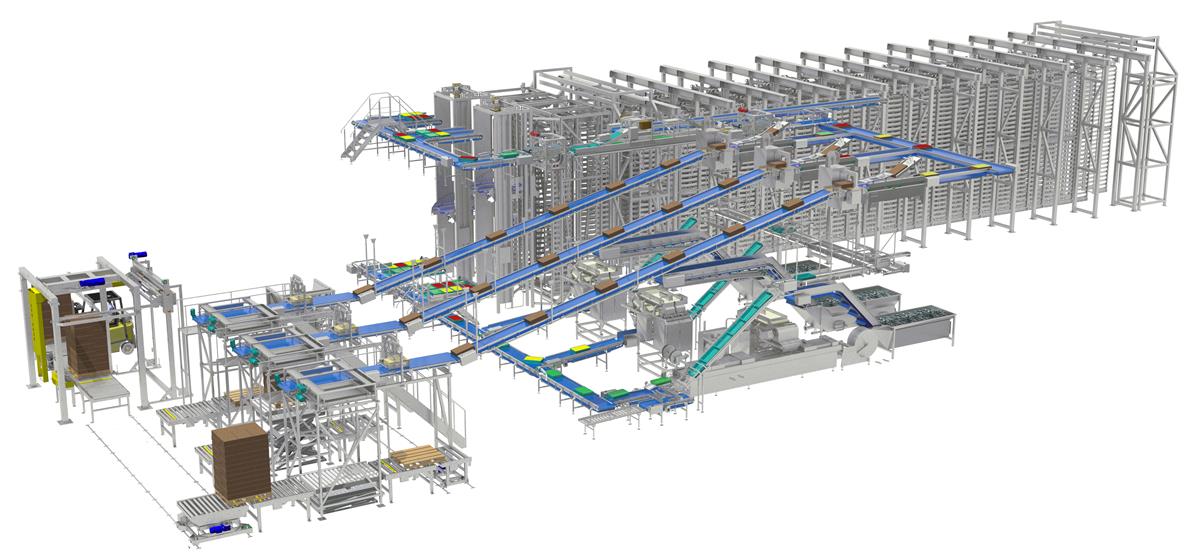
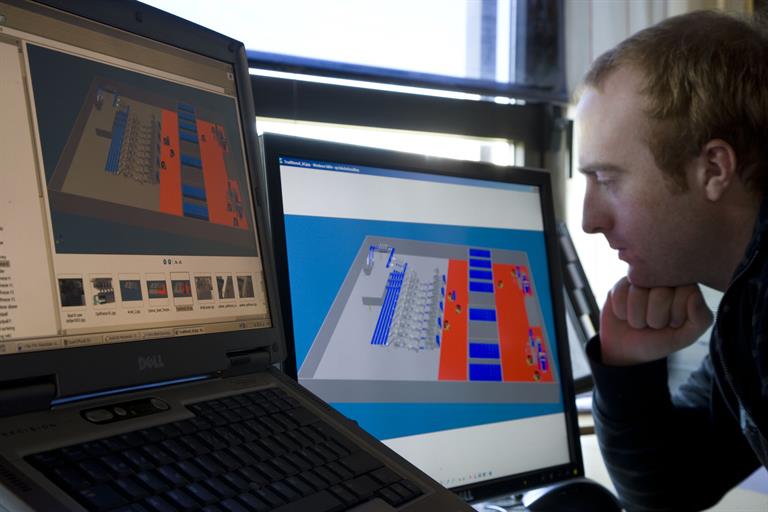
From expertise to innovation
Optimar has a well-established track record of creative success when off-the-shelf options are not options at all. So strong, in fact, that many custom solutions have themselves become must-have, off-the-shelf standards.
.tmb-xl-narrow.jpg?sfvrsn=338efcd0_3)
Sometimes, resolving a design or logistics dilemma is simply a matter of adapting a well-proven solution to meet a special need.
Sometimes, however, the situation requires a totally new vision and Optimar engineers are experts at transforming innovative ideas into realistic solutions.
We have acquired our reputation for creative thinking by developing customized solutions that meet the exacting standards of the ever-changing food processing industry. Over 40 years ago, for example, we helped transform a branch of the industry, fish processing. We did this by designing and delivering the world’s first factory to process fish when they are freshest – on board a ship at sea.
Optimar continues to take the risks that innovative results often require at the beginning. The priorities that gave us the security to venture into totally new territory in the past, remain the same today:
- flexibility
- customer loyalty
- balancing requirements, wishes and budgets
- careful assessment of new technologies
- curiosity

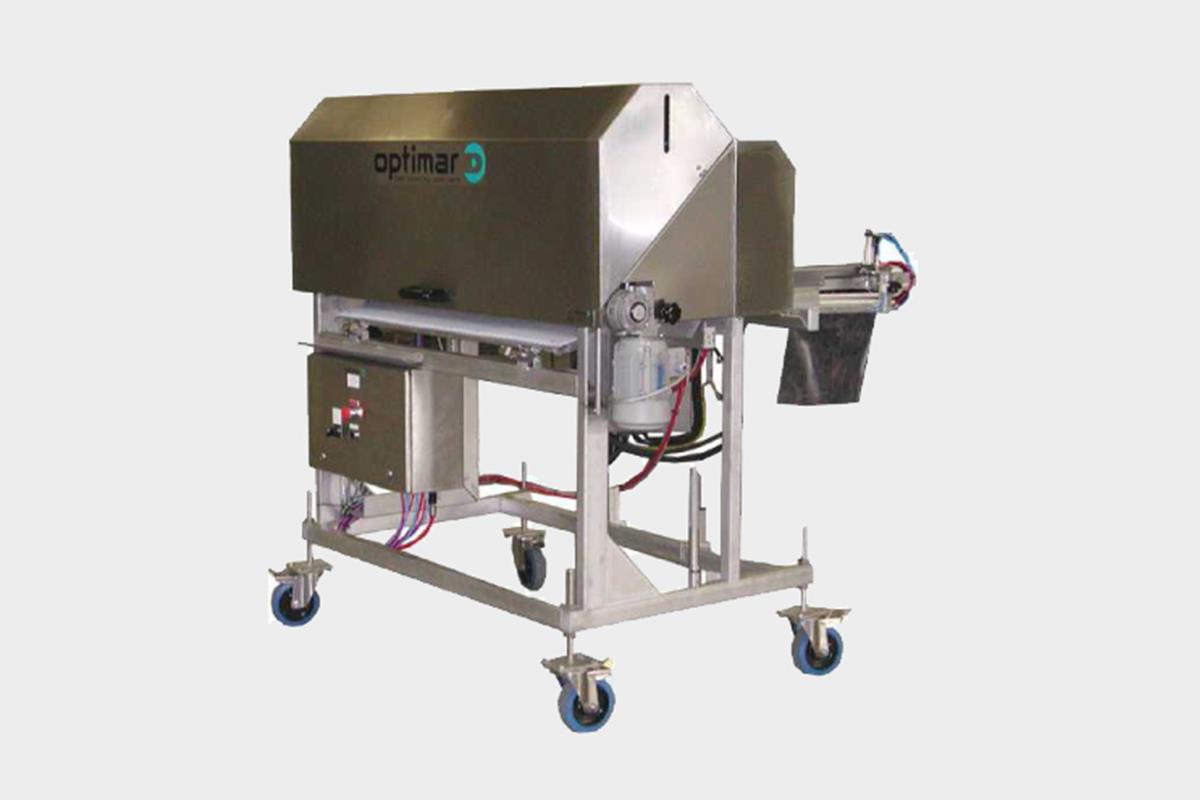
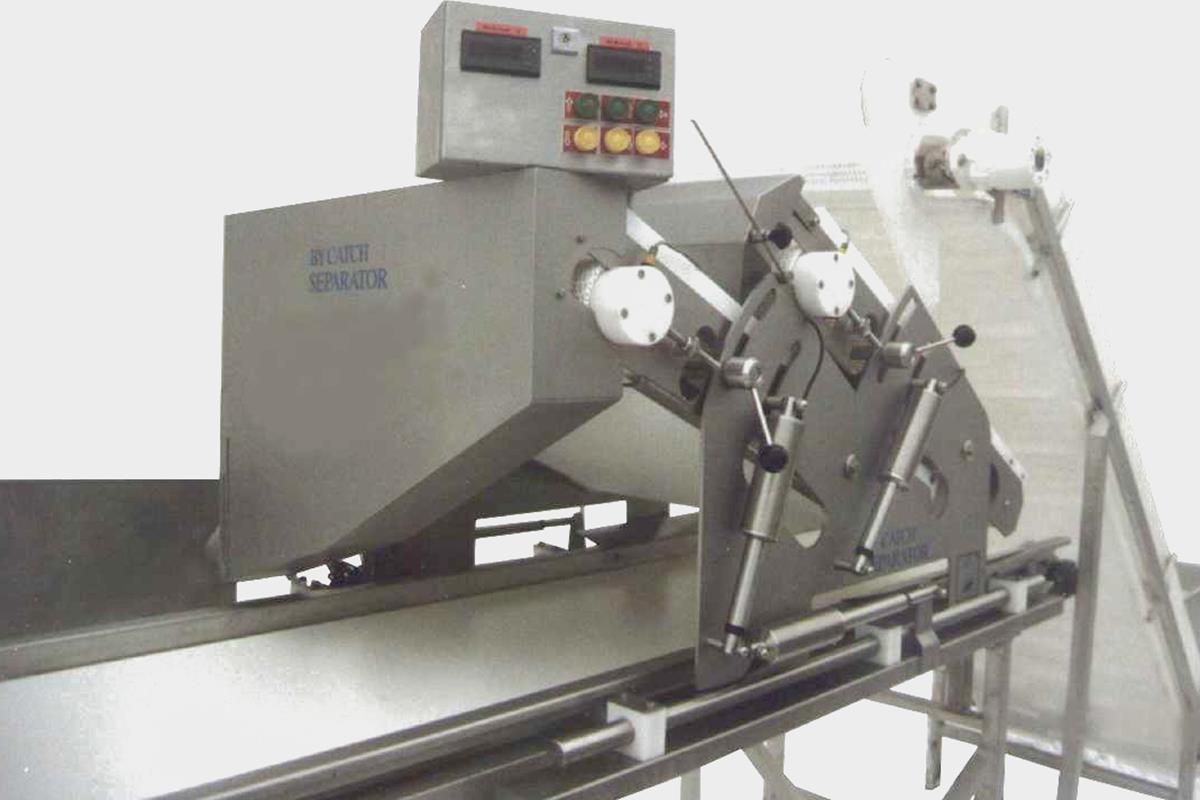
.tmb-lg.jpg?sfvrsn=338efcd0_1)
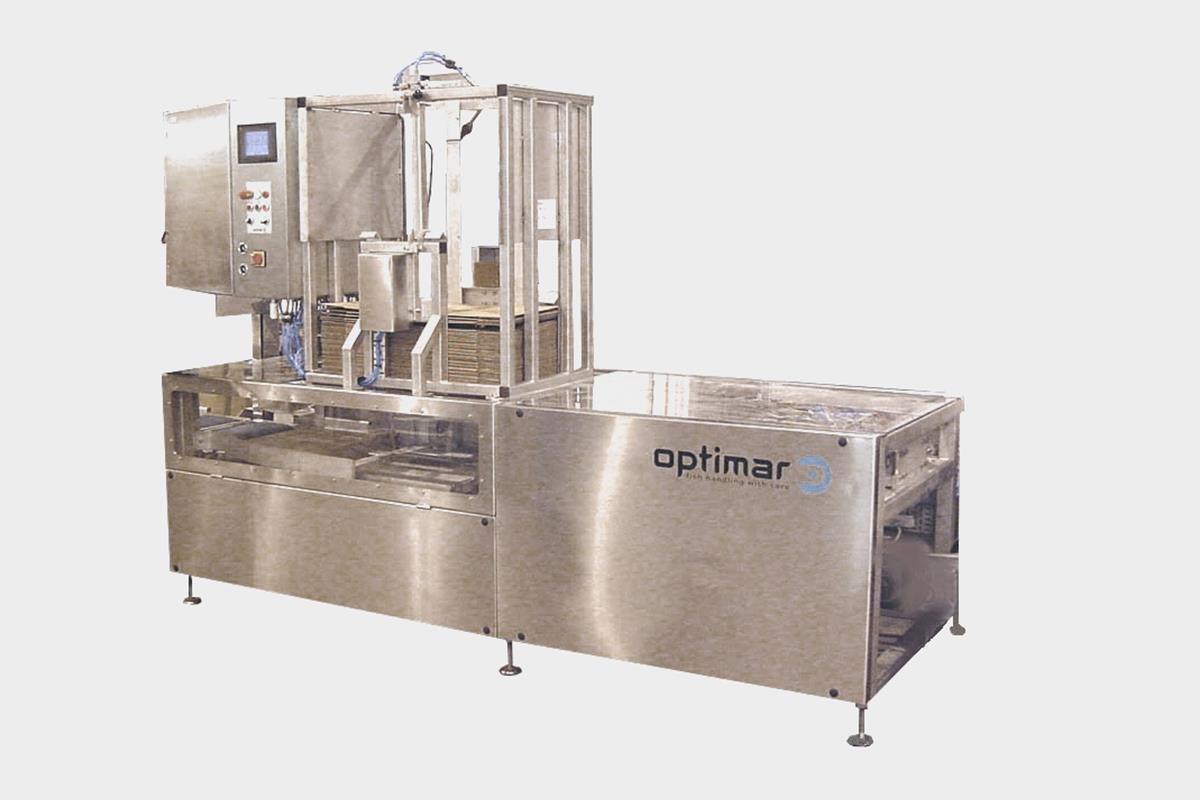

Controlling
Power at your fingertips
Each automatic or robotic Optimar product has its own touch-screen panel to control its operation. The panels may look quite ordinary but, like the products themselves, they are unique.
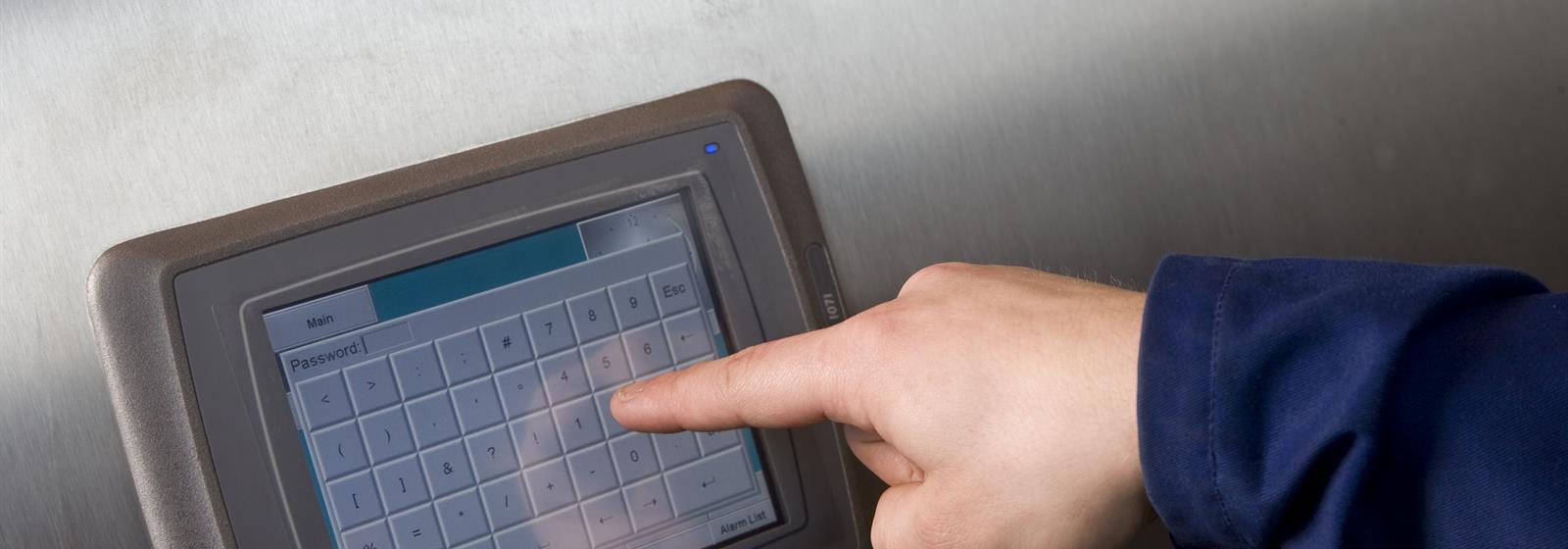
Optimar makes the electrical cabinets and consoles that power Optimar equipment. We use the same high-quality stainless steel, to meet the highest international standards for dust and water resistance
In addition to flexible functionality and options on the inside, they must pass Optimar’s rugged test for durability under extreme conditions on the outside too. For instance, they must function without fail in extraordinary operating conditions that may be damp with humidity, wet with salt water or dry with heat.
Some touch-screen cabinets are fixed in position, some are mounted so they rotate up to 360o but all are positioned at comfortable working heights in the most convenient locations. As a result, they may be specially mounted for unusual equipment configurations and may be distanced from the main power cabinet.
The touch-screen displays are high resolution and in color so they are clearly readable from most angles in any lighting situation. The operating menus vary according to the Optimar product but the basic design and content of each graphical user interface are the same.
Navigation is straightforward and intuitive so even Optimar’s most sophisticated equipment can be easily and safely managed by a trained operator with minimal experience. Depending on the machine, the EasyTouch menu may include options to access capacity information or other performance data over a short period. More detailed, accumulated information is available from OptiControl NetCenter.
Optimar machines with touch-screen panels can be linked to other Optimar equipment and monitored collectively via OptiControl NetCenter for a total network overview.
All EasyTouch menus include:
Language options
English, Norwegian and Spanish are standard options with all Optimar systems. EasyTouch menus are available in other languages upon request.
System and process diagrams
In automatic mode, the operator works from an on-screen diagram of the system showing each step of the process. In manual mode, the operator controls each phase of the process from a display with manual options specific to the phase of operation.
Visible and understandable error alerts
Alarm signals indicating a fault or stop are clearly visible and, in automatic mode, the area causing the problem is precisely highlighted on a schematic diagram.
Behind the screens, ahead of the times
What sets Optimar apart are not just the designs of our processing systems, not just the way we work with you, and not just the solutions that result.
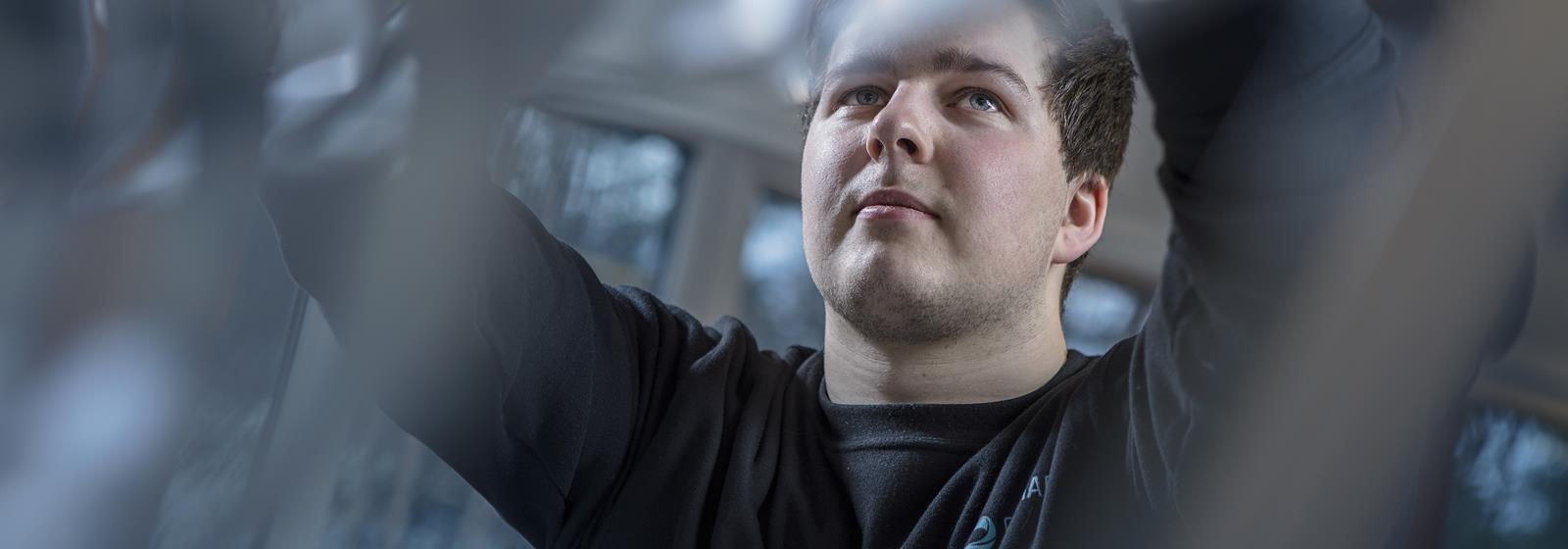
What sets Optimar apart are not just the designs of our processing systems, not just the way we work with you, and not just the solutions that result.
What does set us apart are the systems you don’t see that control the systems you do see.
Optimar’s automation team includes specialists in electronic, pneumatic and hydraulic technologies and a team of software engineers with in-depth skills to synchronize the movements of every part of every Optimar system.
This means the software and operating systems that drive each Optimar machine, processing line or total facility are unique to Optimar.
It also means the systems are understood by an entire team of programmers and specialists, not just one or two, and each person is committed full-time, in-house to fulfilling Optimar’s commitment to you.
Control EasyTouch – machine-specific touch-screen systems to control operation, define default settings, receive alarm signals, examine short-term alarm history, review performance data, and more.
OptiControl ProLine – central logical control systems (PLCs) specific to a processing line, freezing system, palletizing system or other “logical” production area to ensure the workflow is smooth and distribution among the components of the line is optimized.
OptiControl NetCenter – a web-based Production Management Control (PMC) network connecting all Optimar systems for a total overview of real-time and past performance, real versus theoretical capacities, bottlenecks and downtime, alarms and much, much more.
An entire processing facility can be monitored, managed and maintained via the Internet using a computer, personal data assistant (PDA) or telephone with Web access from any location around the corner or around the world. A powerful, sophisticated tool to help ensure your business is achieving its full potential and profit.
Conveying
Up, down,over, under, around and through
Optimar has made thousands of conveyors for use in all types of processes in all types of configurations in all types of production facilities. Seldom has one system been exactly the same as the next.
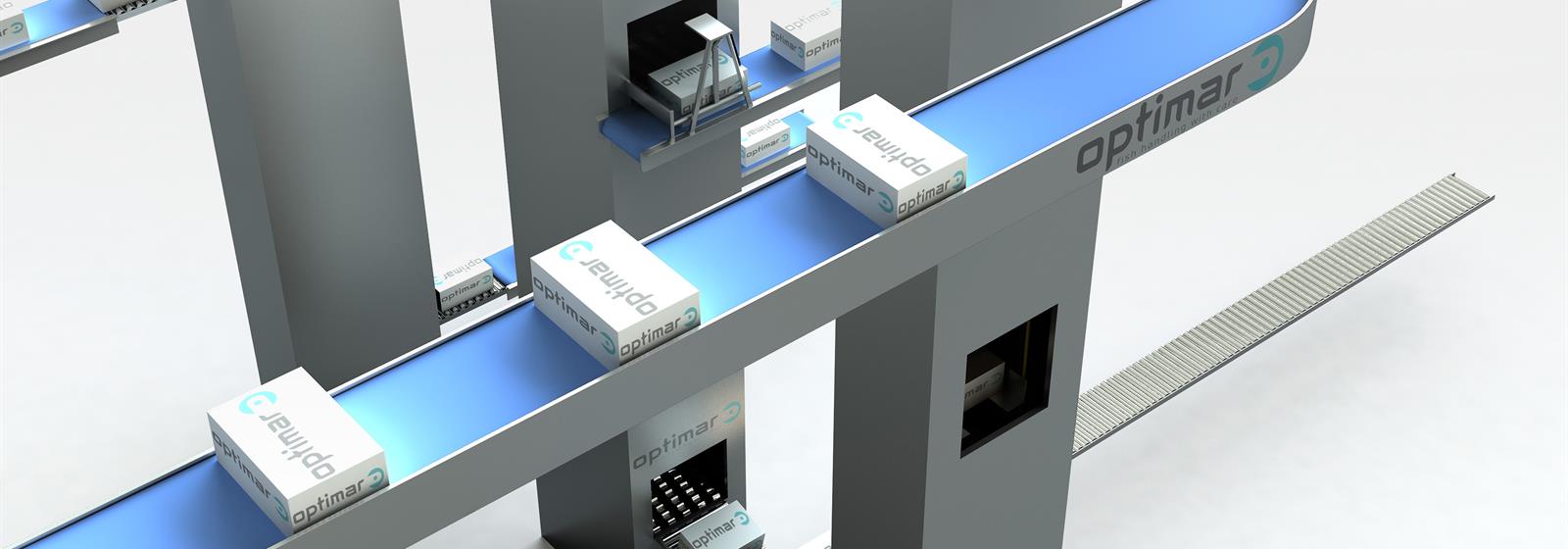
"One size" never "fits all"
The only thing “standard” about Optimar conveyors is that they move products from point A to point B. Beyond this basic function, however, something is always slightly different.
Virtually all Optimar conveyors are a customized combination of size, angle, movement, height, width and/or length. For Optimar – and for you – something as ordinary as a conveyor becomes quite extra-ordinary.
Conveyors are as vital to your processing system as the products they carry from one step to another. Each Optimar conveyor is designed to ensure a smooth, consistent product flow and, at the same time, conserve space and maximize efficiency.
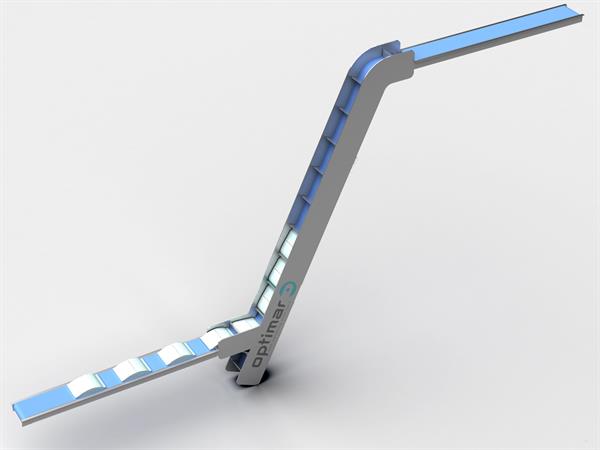

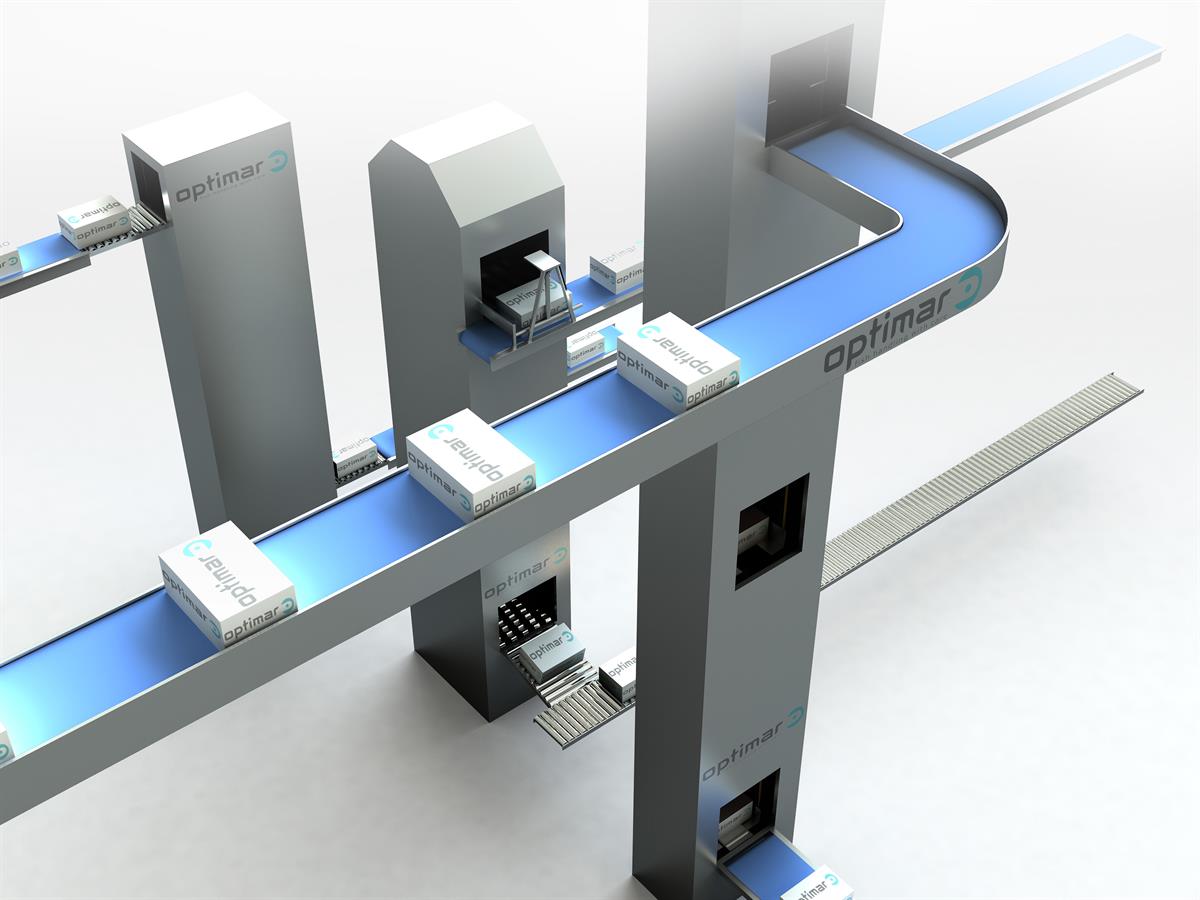
Freezing
Unique designs
Optimar’s H1 and H2 horizontal freezers feature fully automatic technology that opens, loads and unloads only one station at a time. As simple and logical as this sounds, the design is unique to the industry with savings and benefits that are incredible.

Effective use of space
Uses 100% of available height
The fact that only one plate at a time is open can increase the cost-effective use of space by as much as 50%.
H1 and H2 freezers devote the full height of the space available to freezing. Unlike traditional systems, no extra space needs to be reserved for those times in the process when all stations must be fully open at the same time.
In addition, since the H1 and H2 are fully automatic, there are no loading or unloading height restrictions. The sky is really the limit.
Efficient freezing
Hydraulic equalizers maintain constant surface pressures, increasing freezing capacity up to 20%. Pressure on the content of a frame remains constant, regardless of the position of the station (lowest, highest or in between).
When a station is loaded and the plates closed, freezing is immediate, thorough and uniform. As a station is unloaded from one side it is reloaded from the other, saving time and conserving energy.
Energy efficient
Working strategically and automatically one station at a time maintains a continuous load level on the refrigeration equipment. This eliminates the energy-consuming spikes and temperature fluctuations caused by loading or unloading all stations of an entire freezer at the same time.
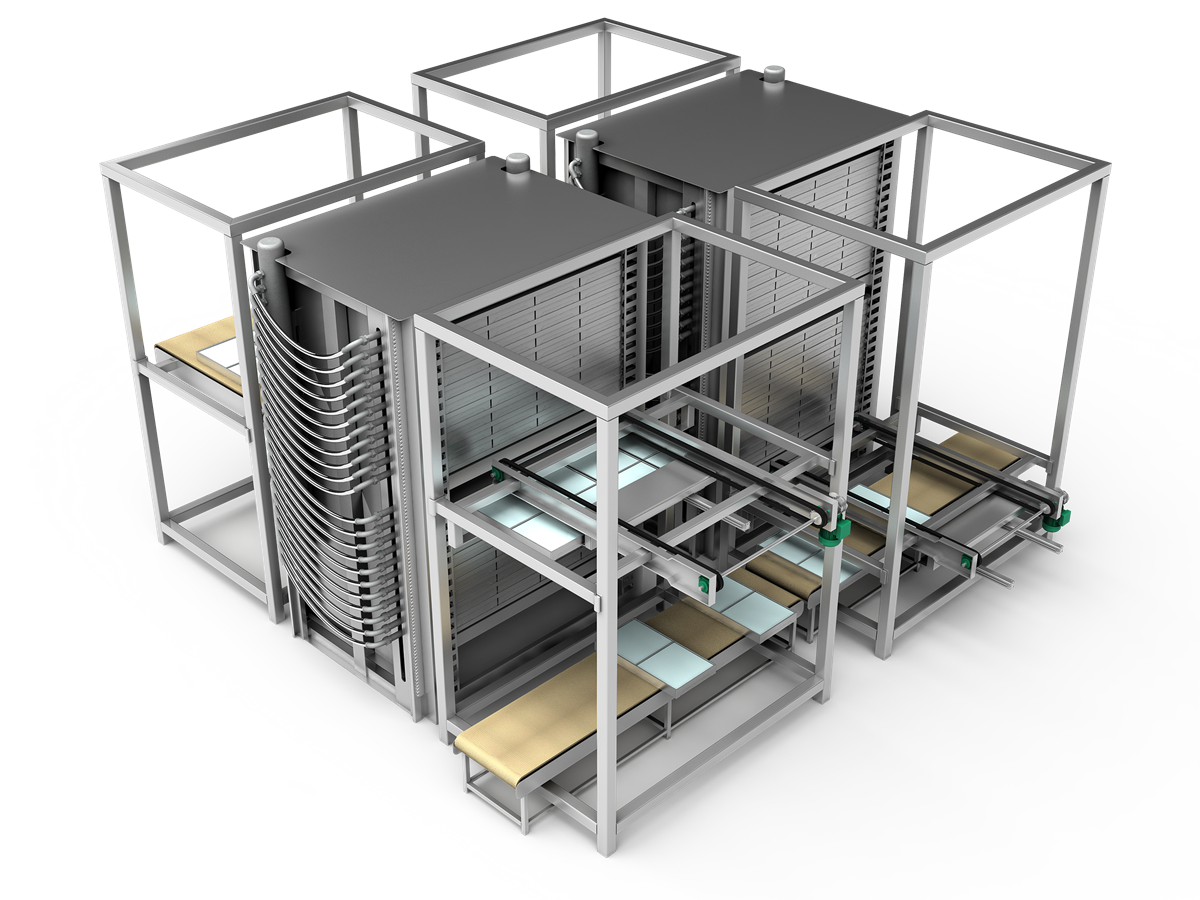
Automatic horizontal freezers
Optimar is unmatched in designing and producing automatic horizontal freezing systems that withstand the tests of time and heavy use in extreme conditions and limited spaces.
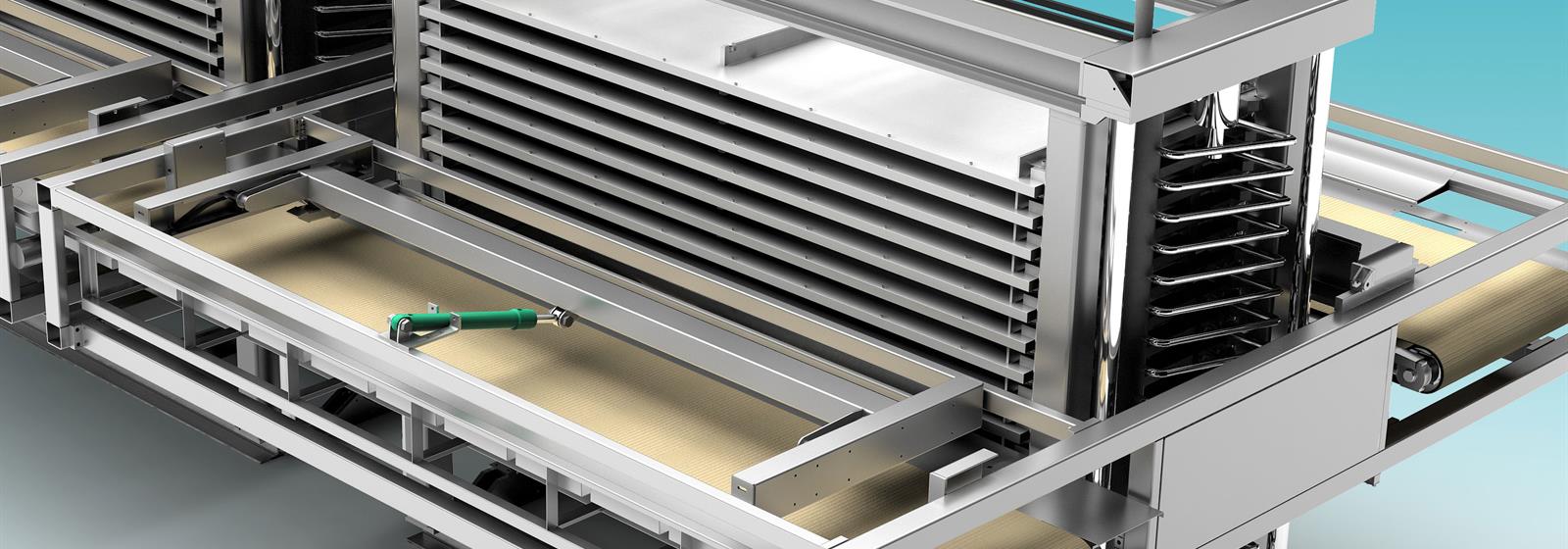
This is proven by the fact that in 1988 Optimar delivered the first automatic horizontal plate-freezers for processing fish on board a ship at sea... and that first installation is still functioning at full speed. The H1 remains the only available freezer of its type and is unsurpassed in performance, reliability and handling capacities.
Automatic systems for vertical freezers
Optimar has several systems for unloading vertical freezers. Each has features that revolutionize the food processing industry.
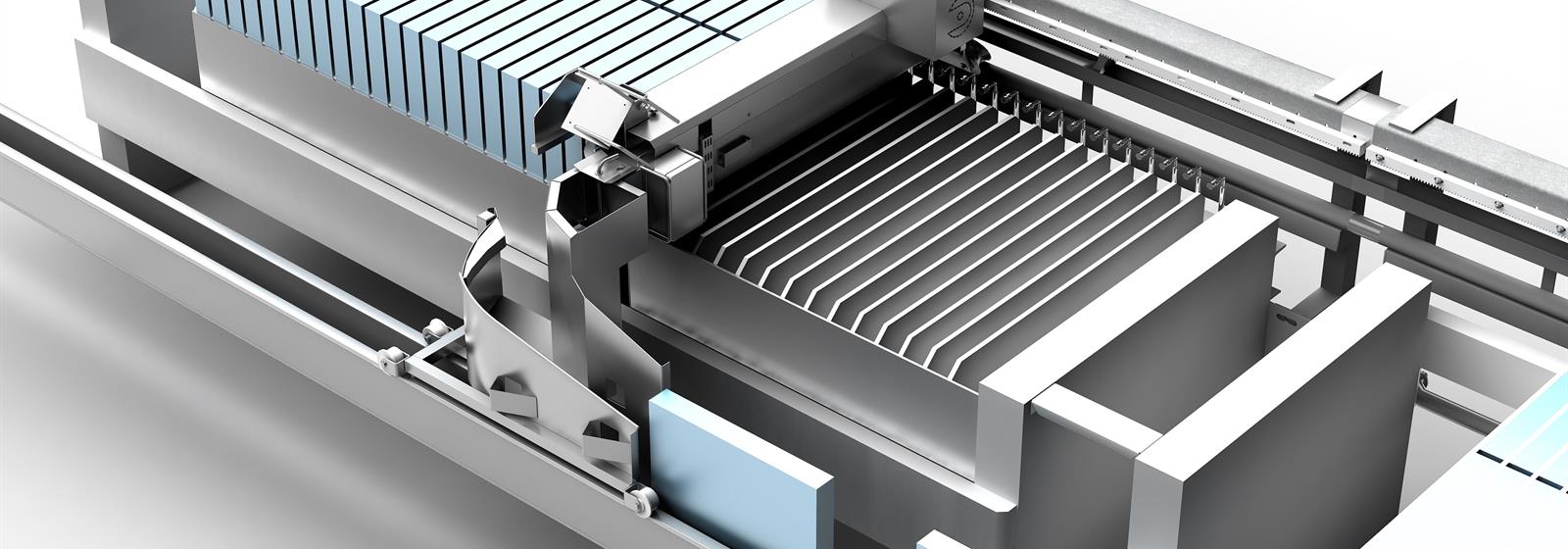
Leading the way
For OptiFreeze, however, these unique features are simply basic standards:
- reliable and durable in all operating environments
- eliminate manual handling of heavy, cold loads
- operate at full potential in limited spaces
- ejector technology releases frozen blocks without warming, defrosting
- no risk of leakage
- off-loading conveyor takes very little space
All Optimar vertical-freezer solutions are designed to handle two half-blocks or one whole and transport them at heights above floor level that ensure safe and clean handling. Unlike most systems, the Optimar units can service an entire line of freezers rather than only one.
Each of the systems is designed to be installed wherever a person can stand. They require no extra ceiling height, for example, and they can easily be positioned to handle space limitations caused by pillars, bulkheads or other equipment.
Optimar’s unloading solutions for vertical freezers eliminate the use of electrical sensors that areoften unreliable in extremely cold environments.The unloading units are separate from the freezer, however, so freezing can continue if the unloader is down.
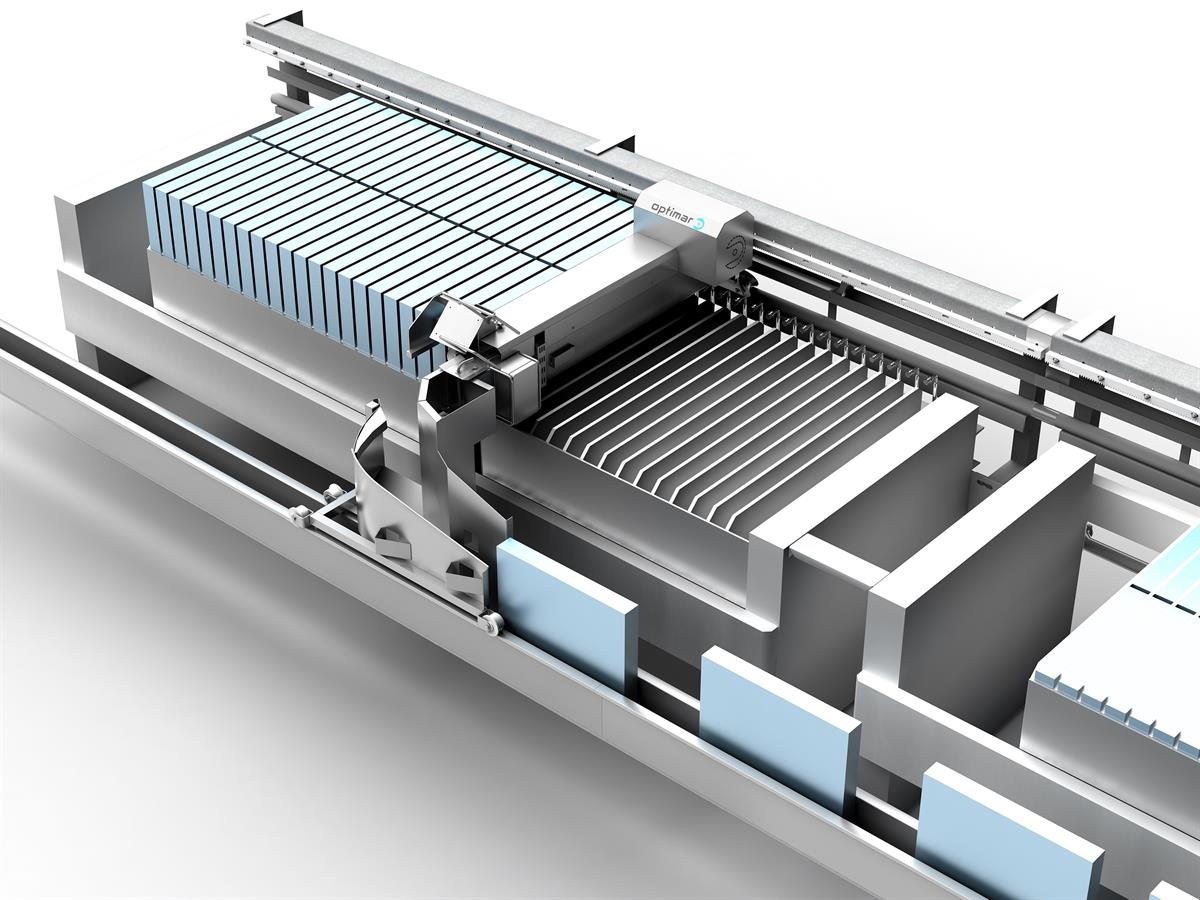
V1
Fully automatic side-ejection system. Requires compatible vertical plate freezers.
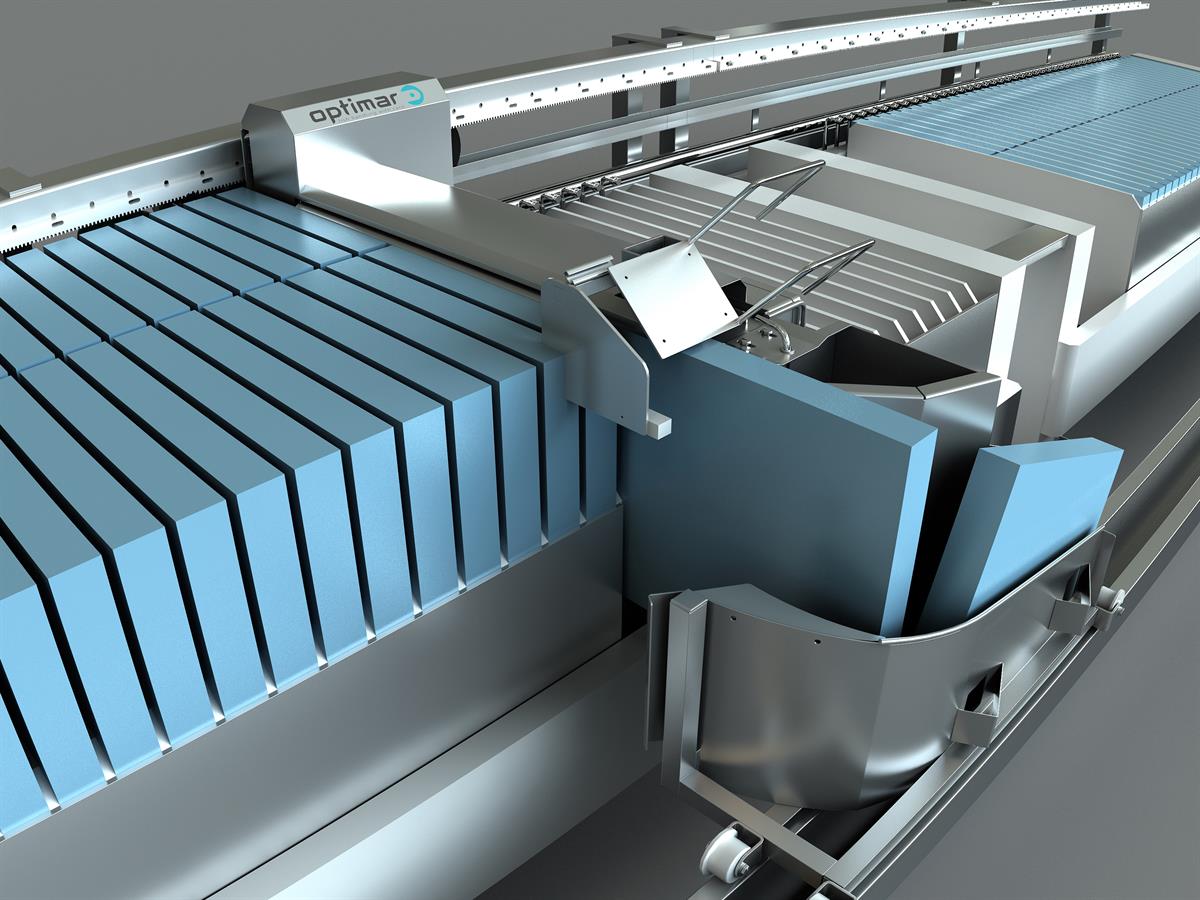
V2
Semi-automatic side ejection system. Requires compatible vertical plate freezers.
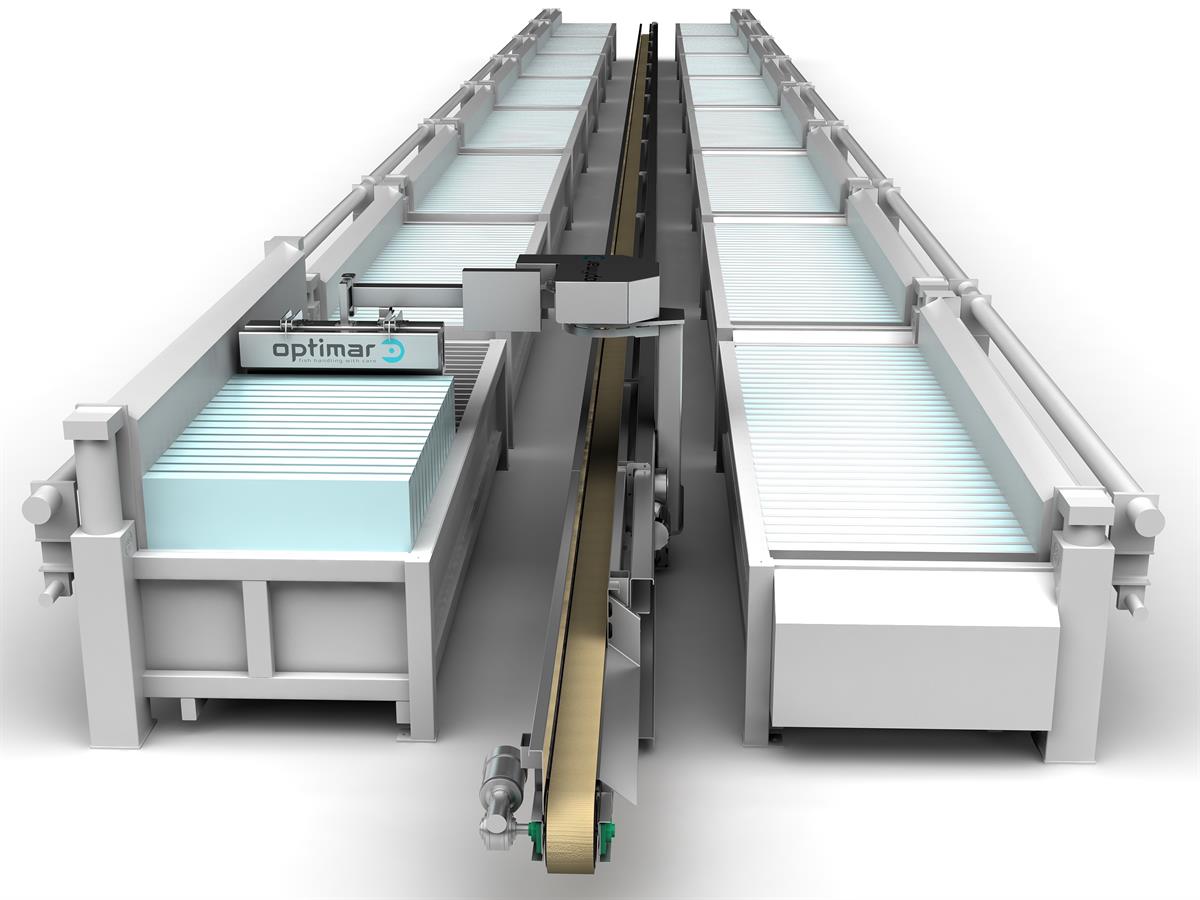
V3
Fully-automatic unloading system using one robotic arm to off-load blocks (two halves or one whole) from two freezer lines. The robotic arm can move along the lines in either direction and can be used with any standard vertical plate freezers.
One success leads to another
Optimar’s goal has always been to continuously improve our products so you can improve your food processing efficiency, safety and profitability.
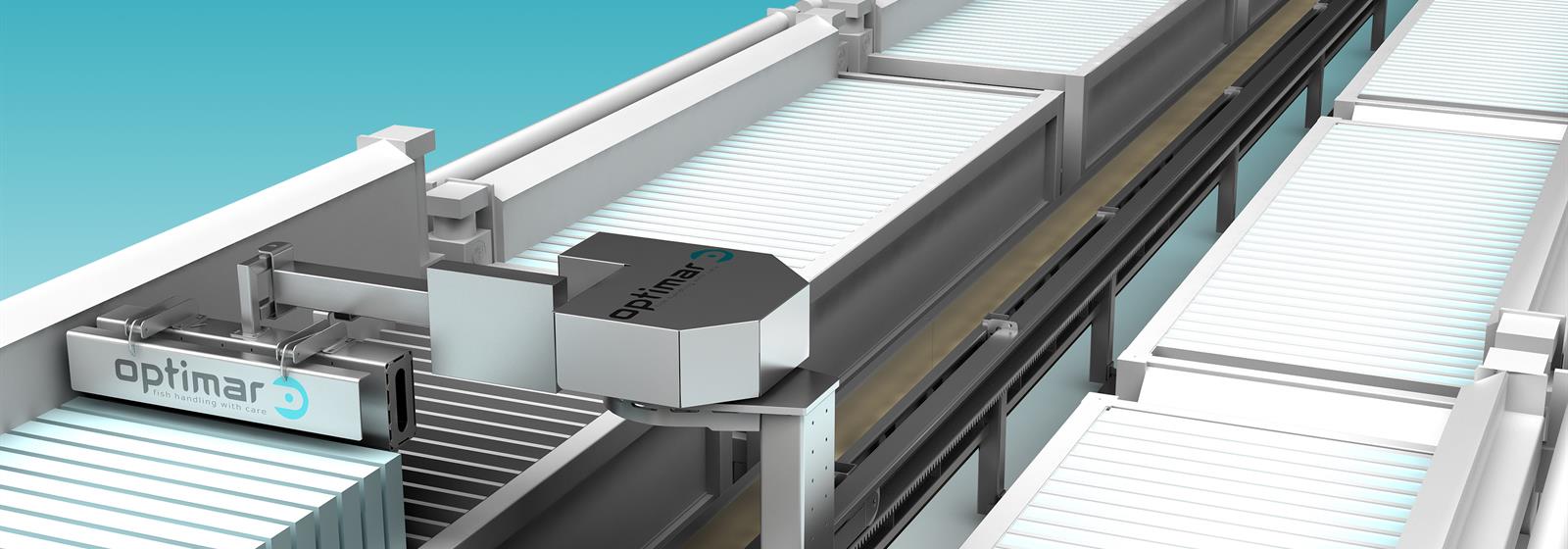
We use the experience and expertise we gain by successfully solving one challenge to confront and overcome another. As a result, we develop solutions that lead the way in design, technology, handling and capacity.
Example: 36 freezers positioned in four lines of nine freezers each.
Again...
In 2003, Optimar developed the first fully automatic vertical unloading system for use on board a ship. One automated unloader can service an entire line of freezers placed in a row of any length.
36 OptiFreeze-compatible freezers
NOK 14.4 million
4 unloading units (one per line)
NOK 2.6 million
Total cost: NOK 17.0 million
And again...
In 2005, Optimar developed a semi-automatic version of the fully automatic vertical unloading system. The modified system still eliminates manual handling of heavy loads and services the same number of freezers in the same alignment but substantially reduces the price.
36 OptiFreeze-compatible freezers
NOK 9.9 million
4 unloading units (one per line)
NOK 2.6 million
Total cost: NOK 12.5 million
And again...
In 2008, Optimar released a fully automatic robotic system to unload vertical freezers. One robotic arm services two lines and can be used with any standard freezer. This makes it the perfect solution for upgrading an existing processing facility, on board or on shore. For example, two robotic arms can service four lines of freezers, in theory up to any number in length.
36 standard freezers in an existing plant
NOK 0.0 million
2 unloading robotic-arm units
NOK 3.0 million
Total cost: NOK 3.0 million
Automatic plate freezers
Optimar’s automated vertical and horizontal plate-freezing systems are available in a variety of types, sizes and capacities but all solutions offer the same major benefits
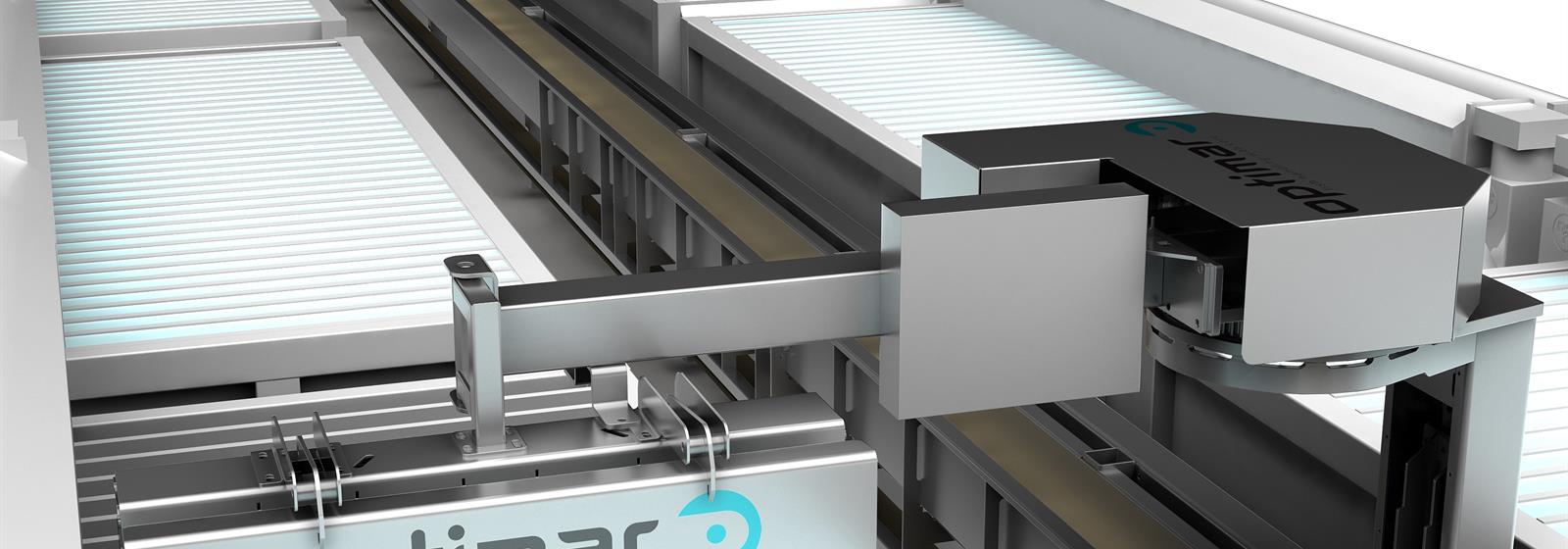
Safe, healthy work environment
OptiFreeze solutions eliminate:
- prolonged, repeated exposure to cold, humid air.
- manual lifting of heavy, hard-to-handle frozen blocks.
- repetitive, difficult movement in limited spaces.
Site hygiene and satisfied consumers
OptiFreeze stainless steel, non-corrosive frames, hoses and plates ensure:
- easy cleaning, sanitizing and maintenance.
- steady, uniform temperatures throughout the processing cycle.
- gentle handling to prevent product damage (bruising, staining, breaking, defrosting, etc.).
Increased productivity and profitability
OptiFreeze solutions are cost-effective from the start:
- high-performance units independent of new or existing refrigeration systems.
- durable and reliable even in the toughest conditions at sea or on shore.
- back-up plans are always in place to ensure a steady workflow.
- interface with all types of coolants, including those safest for the global environment.
- easier to recruit and retain labor.
All OptiFreeze systems may be monitored and managed using OptiControl NetCenter:
- provide real-time data regarding capacity, input, output, etc.
- exchange up-to-the-minute information via the Internet.
- provide real-time data regarding capacity, input, output, etc.
- exchange up-to-the-minute information via the Internet.
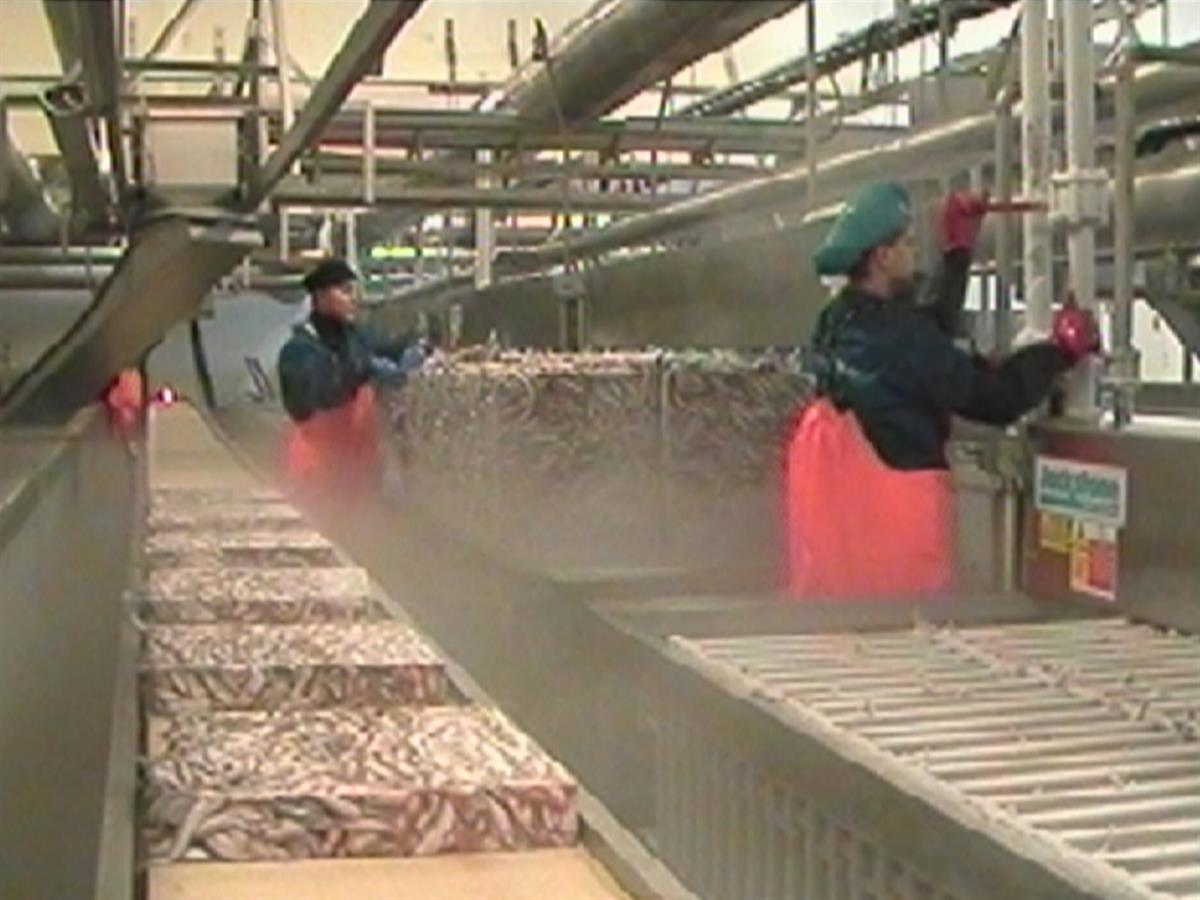
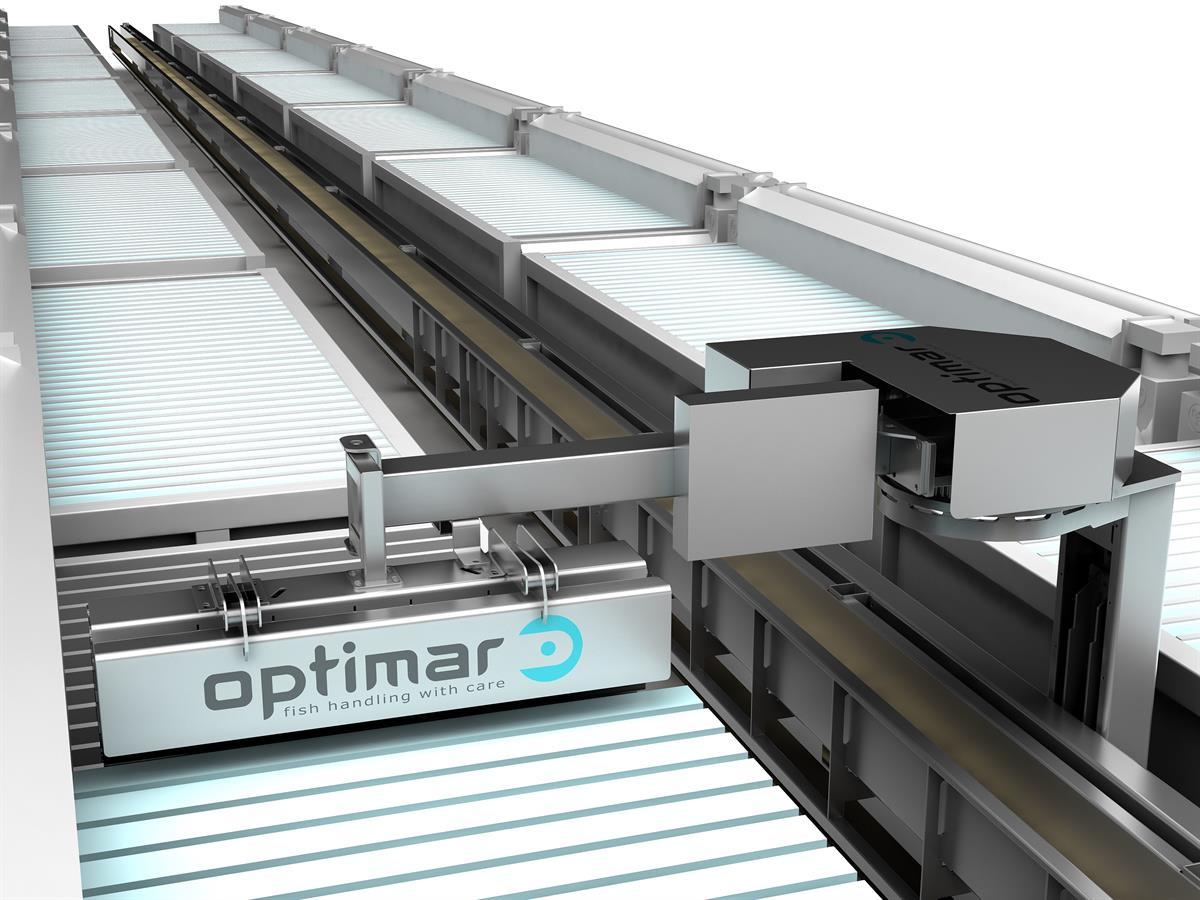
Start! increasing efficiency, capacity, profitability
Automatic Freezing Solutions
In 1988, Optimar delivered its first – and the first – automatic, horizontal plate-freezing system designed exclusively for processing fish onboard a vessel at sea.
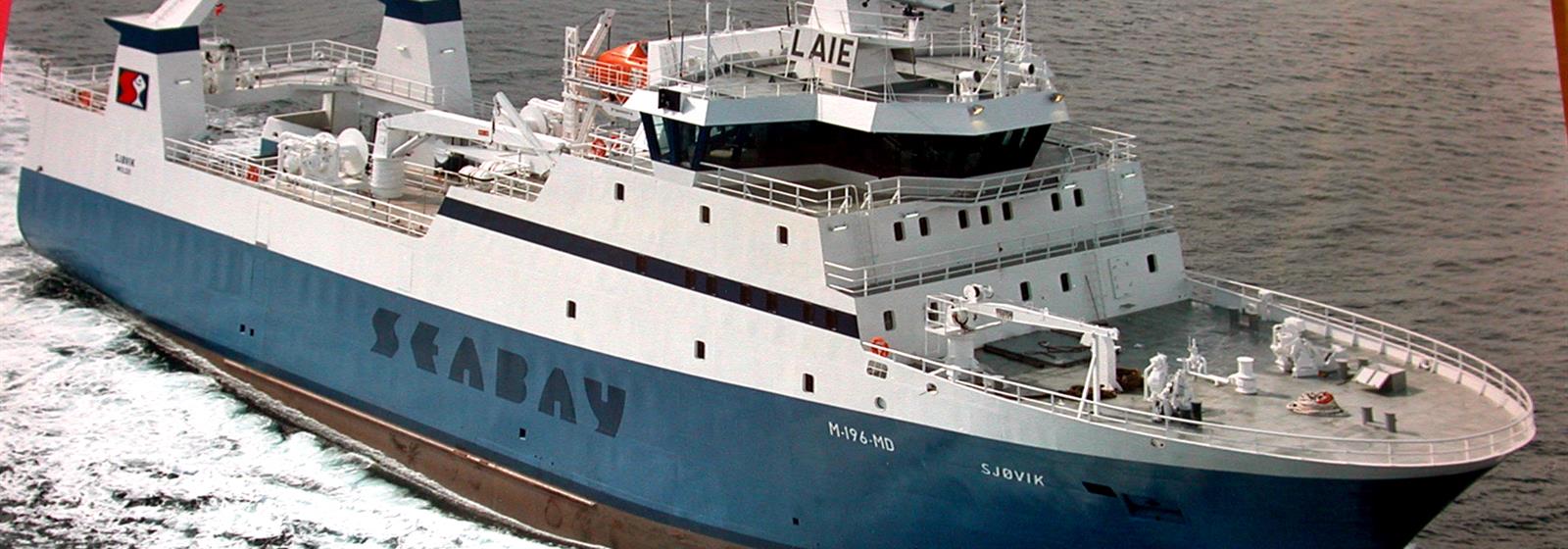
Always a step ahead
Today, many development generations and units later, on land and on board, we’re still going strong... and so is that first unit.
All solutions are based on standard refrigeration and coolant systems, including hose that best protect the environment. Optimar’s expertise, vision and commitment to quality are well-proven and remain as strong as ever.
Optimar continues to set the standards that others try to copy.
We’ve come a long way since we started but we’ve always stayed a step ahead because we:
- seek to conserve energy and protect the environment.
- customize our designs to fit new or existing needs.
- make the most of the space available.
- strive to ensure health and safety of workers and consumers.
- design solutions to minimize costs, save time and maximize production.
Palletizing
Any product on any pallet
Whether loading box-by-box or layer-by-layer, one pallet at a time or 40 at the same time, Optimar has a palletizing system to meet your needs.
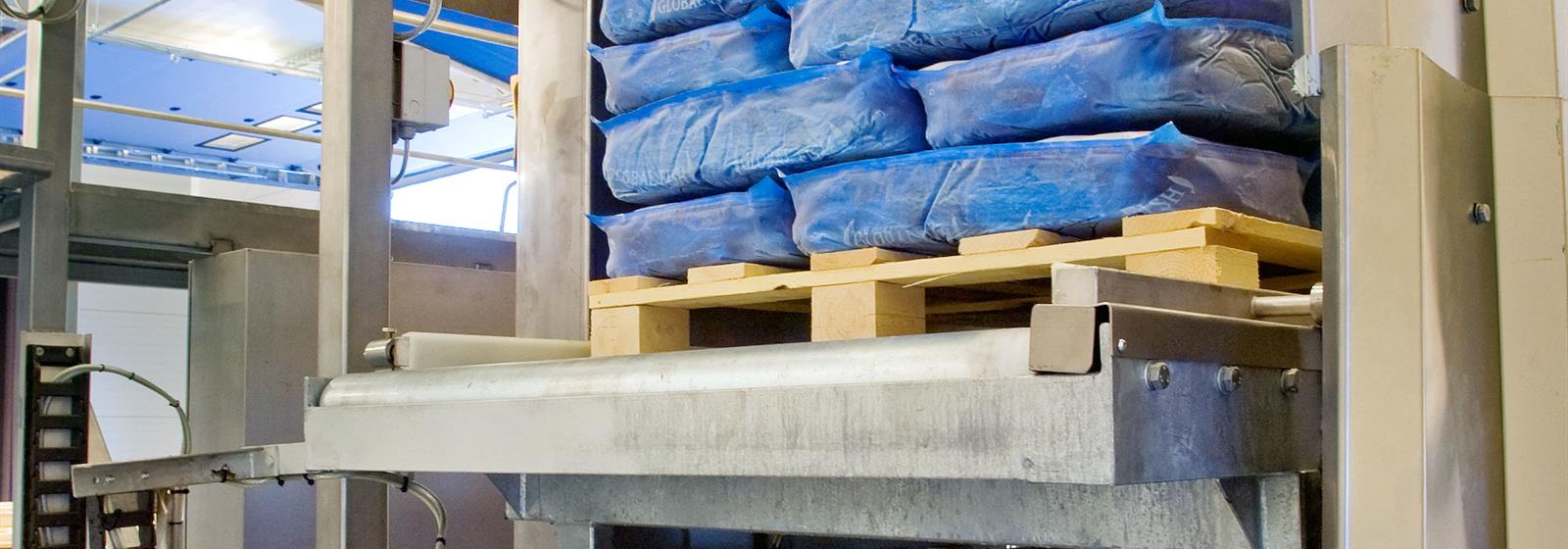
We can do it!
Since even our basic systems far exceed the criteria generally considered “standard” by others, you will soon see why it is perhaps most accurate to say, “we have a customized solution just for you.”
Our background in handling frozen products that are heavy (like a rock) and slippery (like a fish) has helped us develop systems that have incredible power applied so carefully the product is not damaged. We have perfected a few other features too.
OptiPall systems are:
- able to tolerate extreme temperatures, vibration, moisture, etc.
- modular solutions that can be adapted to a wide range of specific products: light or heavy, fresh or frozen, soft or firm, etc.
Optimar takes hands-on care of every part of its unloading and palletizing systems, whether hardware, software, mechanical or control components. They can be serviced via the Internet and easily interfaced with OptiControl NetCenter.
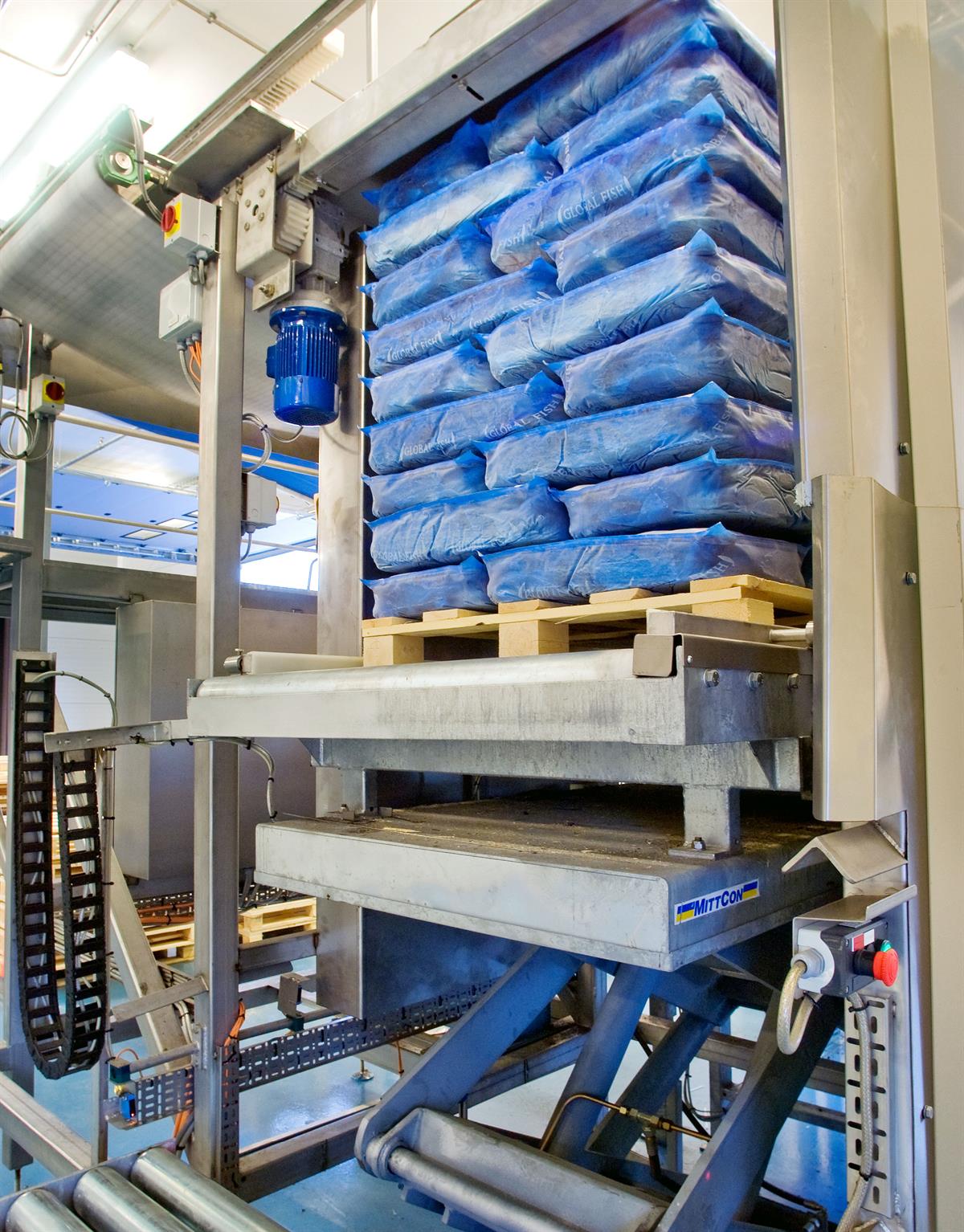
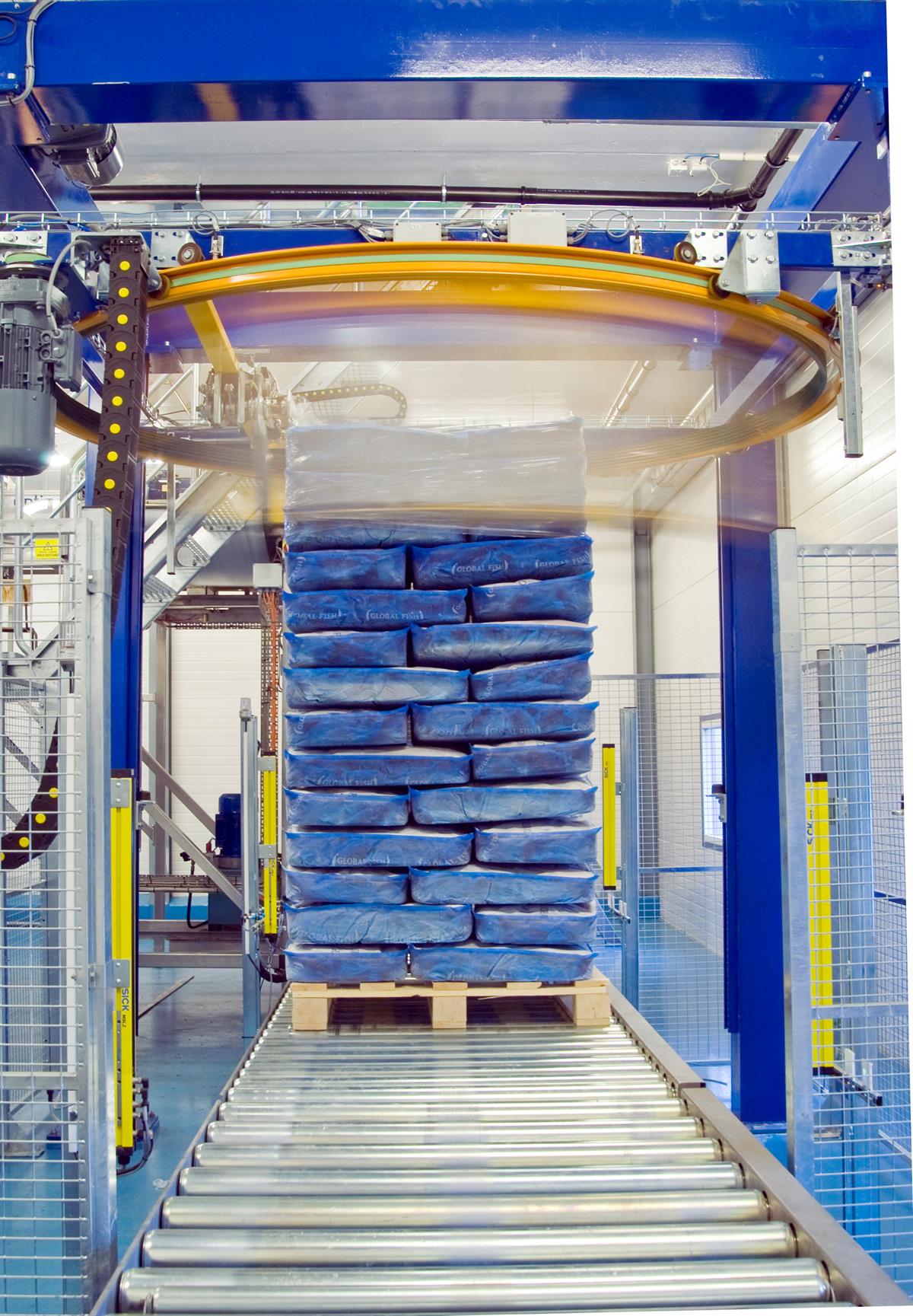
Service
Beyond the call of duty?
"Optimar can’t help you avoid a catastrophe, but they CAN help you recover in record time!" Read more testimonials...
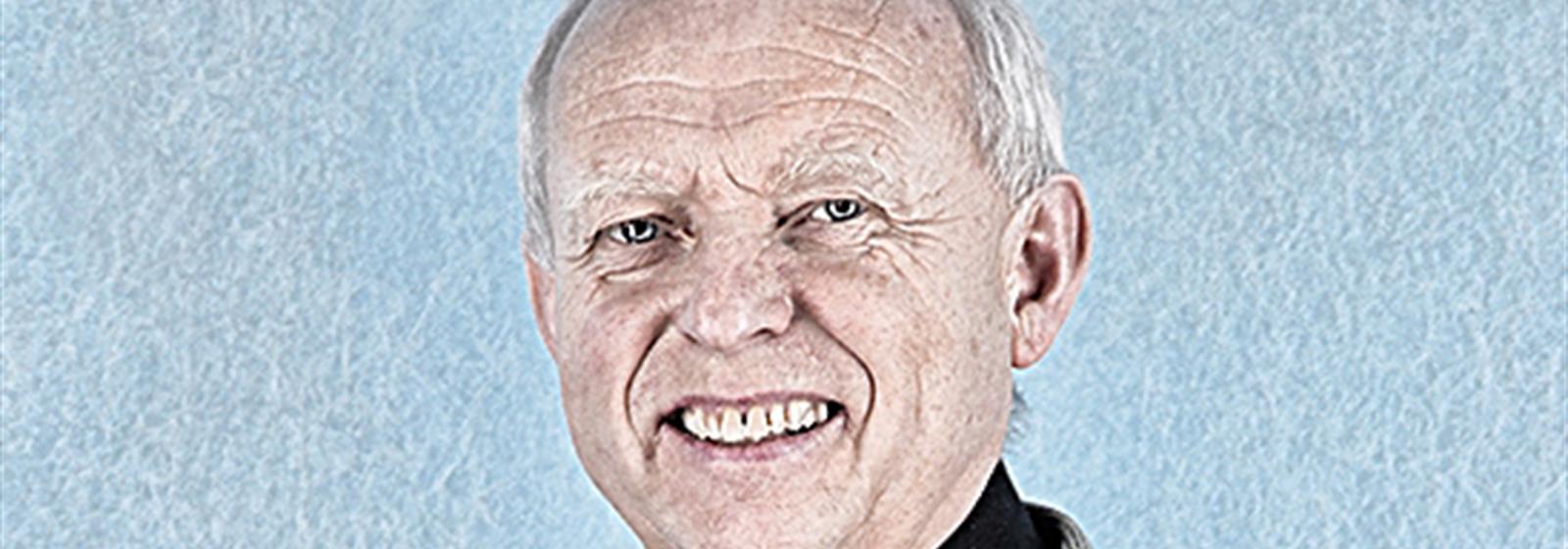
Optimar customers know our machines work in extreme conditions ? they know we do too!
Just as a ship was docking in the calm summer waters of a port in South America, a container ship carrying new Optimar equipment destined to update the vessel encountered the brutal winter conditions of the North Sea. The ship and crew survived the turbulence further north but many containers were lost or damaged, including those holding Optimar’s automated onboard-processing systems built specifically to modernize the ship in the south.
“We assumed the vessel would be out of commission for a full season,” recalls Hitoshi Aita, president of EMDEPES s.a Chile that owns the ship. “This would have meant a tremendous loss of time and income.
“Fortunately,” says Mr. Aita, “Optimar disagreed. They promised to have the vessel up and ready just weeks after the original schedule, something we thought was a ‘mission impossible’ given the time and distance. However, Optimar came through and the ship in South America left the harbor with a fully operational state-of-the-art onboard fish processing plant only fourteen days after the originally scheduled launch date.”
“I was very impressed that a company close to the Artic Circle could re-deliver the equipment to a shipyard in Chile within the given timeframe,” concludes Mr. Aita.

Prompt deliver to the most remote spots
A long-liner fishing vessel enroute from New Zealand needed critical parts for its onboard loading and unloading elevators in order to continue its extended working voyage. Optimar’s first challenge was to machine the parts as quickly as possible. The second and greater challenge was to get the parts to the vessel. The ship’s captain determined that the parts should rendezvous with the ship at the port closest to the point where the ship encountered the mechanical problems. It was vital that the parts be in port and ready for installation the moment the ship docked.
The port of destination was St. Helena, a remote island in the southern Atlantic midway between Africa and South America. The island, a British colony until 1981, is most famous for the fact that Napoleon was detained there from 1815 until his death. For Optimar, an even more important fact was that the island had no airport and was itself accessible only by the Royal Mail Ship, sailing at intervals from Cape Town, Walvis or Ascension Island.
The parts took the most direct air and sea routes possible and arrived in St. Helena well ahead of the vessel. Half a world and ocean away, Optimar delivered the order with the same precision it made the parts.
Shipping address:
The Island of St. Helena South Atlantic Ocean
Coordinates:
15o57”S, 5o42”W
Population:
4255
Area:
420 sq. km
Optimar can’t help you avoid a catastrophe but we can help you recover in record time
In November 2007, at the peak of the fishing season, a fire in an electrical cable-trace at the Norway Pelagic factory in Bodø, Norway, stopped the entire factory and caused considerable damage to the processing equipment.
Before the ashes were cold – and that doesn’t take long above the Artic Circle – it was clear that the process of putting out the fire had caused a strange chemical reaction that left all the stainless steel equipment covered with acid spots.
Fortunately, there were no injuries but with the holiday season approaching the loss of time and income for the employees as well as the company was as damaging as the loss of the machines.
When Optimar was called for advice, technicians were on site immediately, assessing the damage and determining what to replace and rebuild to get the company up and running as quickly as possible.
With round-the-clock, well-coordinated efforts by Optimar’s production and service teams, Norway Pelagic’s own crews and local suppliers, Norway Pelagic celebrated the new year in a fresh, clean, rebuilt facility – less than a month after Optimar received the emergency call for help.
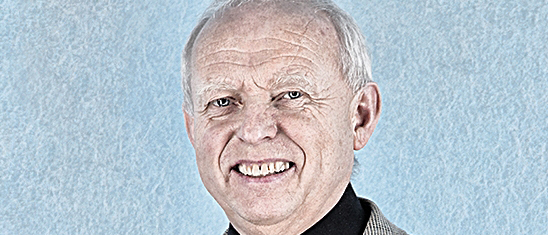
Prevent a minor problem from becoming a major crisis
No matter how good your Optimar equipment is – and we think it is the best – problems can and will occur, especially when it is run at full capacity in extreme conditions in even more extreme environments.
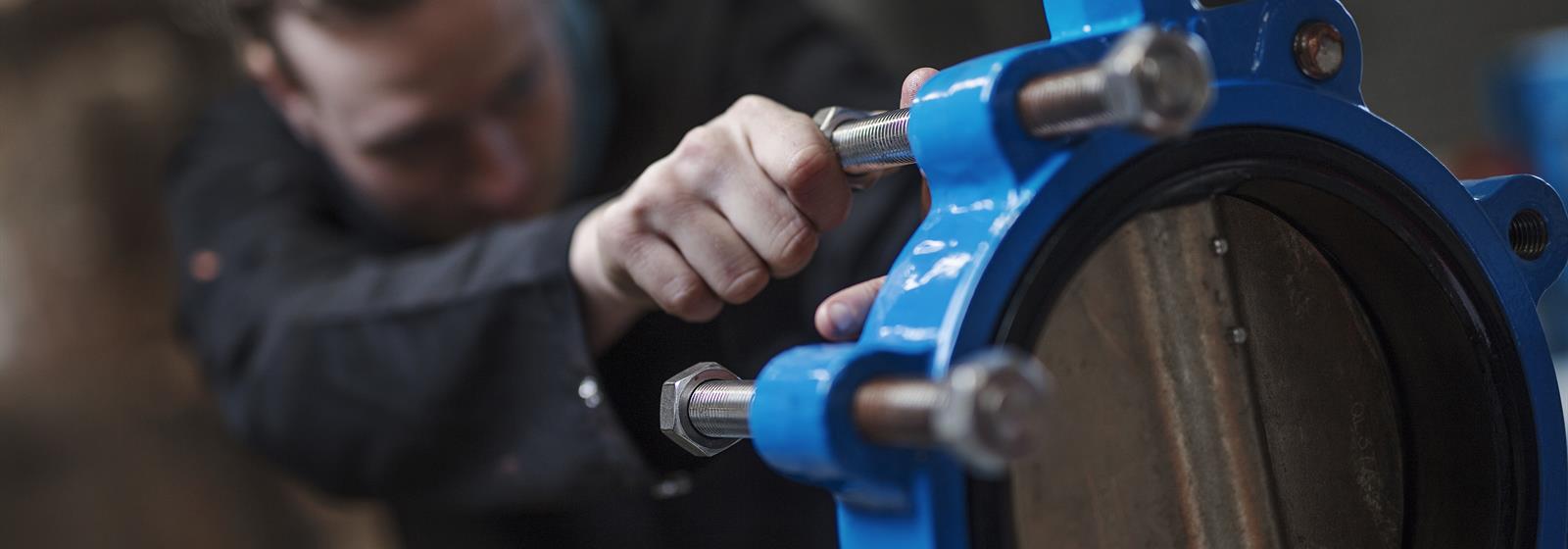
We can’t predict everything that might happen or when, but that doesn’t keep us from being proactive in trying to prevent unplanned downtime and production surprises.
Based on our accumulated histories and expertise, OptiService has developed preventive maintenance schedules for all Optimar equipment, from the most basic conveyor to the most sophisticated robot.
All newer Optimar machines, for example, are equipped with software that monitors the operating time and parts that should be serviced or changed accordingly. Just like a car, each machine requires different levels of maintenance at different timesdepending upon factors such as the intensity of the work load and the products being handled.
Without preventive maintenance, the risks for fatal failure, spoiled products and, as a result, the costs for lost production increase dramatically. We don’t want to take that risk and we don’t want you to take it either.
Replace a part before it fails or after?
It may be hard to believe but preventive maintenance leads to significant short- and long-term savings. Numerous studies and real-life histories show that preventive maintenance:
- improves system reliability
- decreases cost of replacement
- decreases downtime
- improves management of spare parts inventory
An OptiService Agreement is as durable and reliable as all Optimar products. We work closely with you to keep your Agreements up-to-date and functioning as well as the equipment they protect.
OptiService works very hard to strike a balance between your risk – the cost associated with a failure – and the time between preventive maintenance visits.
When equipment doesn’t work the product doesn’t flow and neither does your profit.
Components that wear out are candidates for preventive maintenance. When the cost to repair or replace a component before it fails is less than the cost to replace the component after it fails, it makes sense to maintain the component preventively.
Source: Reliability HotWire, issue 96, February 2009
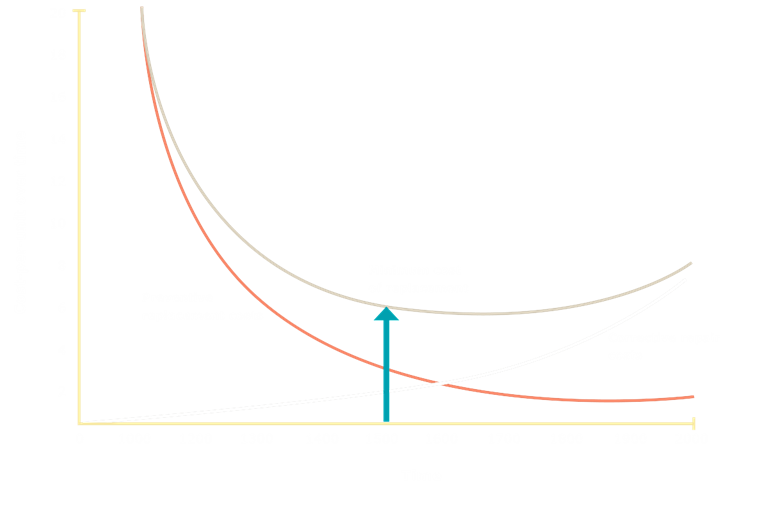
Comprehensive, reliable, guaranteed
Optimar’s innovative service plans are designed to ensure you stay up and running or quickly recover if you aren’t.
.tmb-xl-narrow.jpg?sfvrsn=349bfcd0_3)
OptiService Agreement
Each agreement is tailor-made to ensure that the right service options are combined in ways that best match your specific processing needs. All agreements, however, are based on Optimar’s fundamental guarantee:
Details in an OptiService Agreement may vary according to the type of production, the location of the facility, the level of automation and technology, the use of new and existing equipment, and even the current activities of your closest competitors.
Optimar applies the same creative problem-solving approaches to its service agreements as it does to each of its products and each of your challenges. The results are what set us apart:
- Spare-parts leasing programs.
- Price guarantees.
- Online webshop for one-stop spare-parts ordering or browsing.
- Remote diagnosis and resolution of a problem by phone and/or Internet.
- Individualized preventive maintenance plans.
- Notification of changes in local, national or international regulations or standards.
- Analysis of existing equipment to upgrade, relocate or replace.
- Operator training.
An OptiService Agreement is as durable and reliable as all Optimar products. We work closely with you to keep your Agreements up-to-date and functioning as well as the equipment they protect.
Any part, any time, any place
It is not unusual for a supplier of small- or large-scale equipment, like Optimar, to include a spare-parts package of components in a product delivery.
It is very unusual, however, for you to have theopportunity to specify the contents of the package.
It is even more unusual for you to have the opportunity to lease the package and pay for a part only when you use it.
Whether this week, this month or this year, you pay for parts only as you use them.
Full-time service from a full-time partner
Optimar is itself a full service team and OptiService is a vital player from the very beginning. The way we play the game, however, there is no final whistle – we’re here to stay and to help you at a moment’s notice.
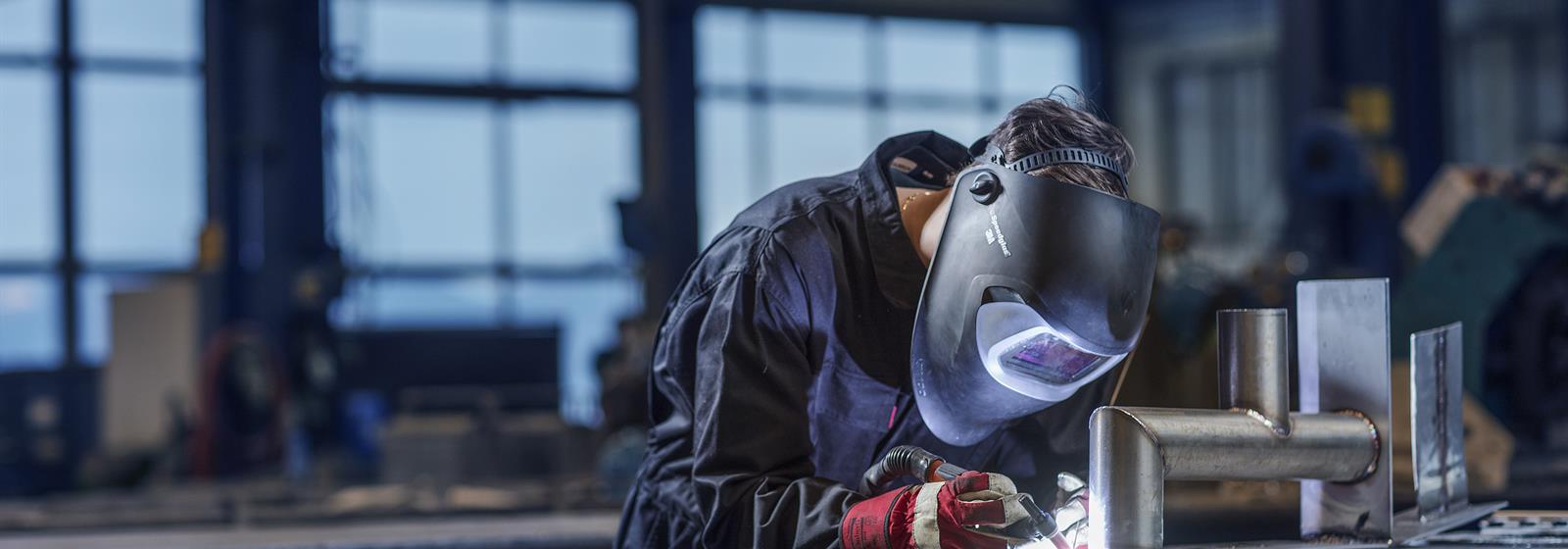
These are facts-of-life in the processing industry and Optimar takes them as seriously as you do.
These are the reasons why OptiService is a well-defined Optimar product and, like all our products, one we stand behind long before and even longer after your purchase is complete.
Our service technicians have hands-on, real-life, real-time experience with everything we supply; from conveyors, freezers and palletizers to the nuts, bolts and gaskets that hold them together to the software that controls them.
Optimar’s designers, system engineers and sales representatives not only recognize the value of this practical experience, they depend on it. They work just as closely with our service staff as they do with you to determine the best ways to meet your needs and requirements.
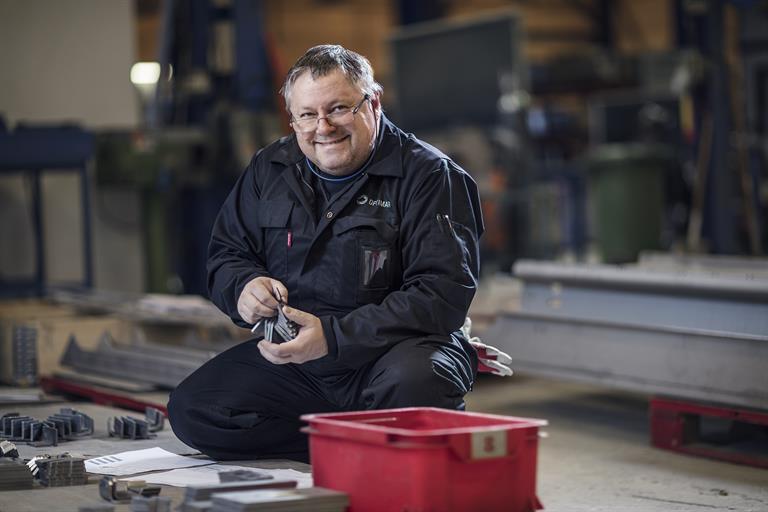
Fact
At one time or another, every penny of your profit passes on, to or through the Optimar equipment you own.
Fact
Whether you are processing fish, chicken, spinach or hot dog buns, time and timing are critical factors to ensure freshness, quality and consumer health.
Fact
Downtime is not an option!